Baoding Guokun is a professional motor castings factory of motor shell, motor housing, and motor casing with tight tolerance, no leakage and wear-resistance in grey cast iron and aluminum alloys.
The motor shell is the outer motor housing to protect the internal motor components from dust, moisture, and other environmental factors while also helping to dissipate heat generated during operation. Essentially, the motor casing is the motor outer shell that holds everything together and safeguards the inner workings.
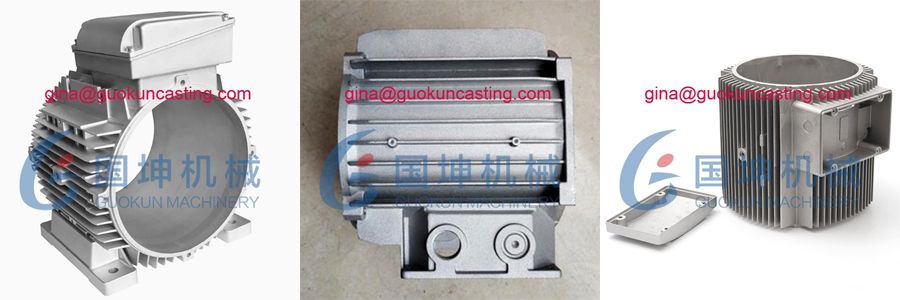
Aluminum motor parts
Aluminum alloy for die casting motor cover:
Die casting material: ADC12, ADC10, A380, A383, AlSi11Cu3, AC-46100, AlSi10Mg and other aluminum alloys
Due to the high-speed operation when electrical motor working, the excessive temperature generated by motor itself needs to be released. The aluminum alloys will be chosen as the motor casing because that aluminum alloys have a strong heat dissipation capacity.
ADC12 (ADC means Aluminum-alloy Die Castings) is an alloy used in creating die casting components. Also known as A383, this aluminum material has low cost, outstanding machinability and excellent mechanical properties. ADC12 is the most widely used for furniture, electronics casing, motor shell, cylinder head cover, cylinder block, motor cover or motor housing, etc.
JIS ADC12 chemical composition
Cu% | 1.5-3.5 | Improves material strength and hardness |
Si% | 9.6-12.0 | Improves flowability and castability |
Mg% | <0.3 | Endows the material with better corrosion resistance |
Zn% | <1.0 | Improve the thermal stability of aluminum alloys |
Fe% | <1.3 | Helps to enhance the material’s mechanical strength |
Mn% | <0.5 | Relatively low content |
Ni% | <0.5 | Relatively low content |
Sn% | <0.2 | Relatively low content |
Al | Remain | The main component, with a content of no less than 85.0% |
Die casting process for aluminum electric motor housing
Die casting is a metal casting technique used to produce metal components by injecting molten metal (Aluminum alloy, Zinc alloy or Magnesium alloy) into a mould cavity. Baoding Guokun can use this cost-effective metal casting process to manufacture high-quality and complex metal castings with tight tolerances and excellent surface finishes, such as gears, engine blocks, furniture handles and electrical components
The die casting process involves several steps, including mold design, metal preparation, injection, casting and finishing.
No. | Steps | Detail |
1 | Mold design and production | The aluminum die casting mold is usually made from steel or aluminum, which is designed to withstand the high temperatures and pressures. Please mail the 3D drawing in .stp, .step or .X-T to Baoding Guokun. They will design the mold by CAD and produce it by CNC machine. |
2 | Metal preparation | Prepare the required aluminum alloy, magnesium or zinc alloy for injection. The alloy will be melted in a furnace and then poured into a ladle. |
3 | Injection | Inject the molten alloy into the mold under high pressure. The molten metal will fills the mould cavity and cools to create the desired shape. |
4 | Casting | After the desired parts has cooled and hardened, open the mould to eject the parts. Please ensure that the part has cooled entirely before handling to avoid any potential injuries. |
5 | Surface treatment | Surface finishing plays a vital role in die casting, as it can impact the durability and function of the part. Standard finishing processes include anodizing, powder coating. |
Advantage and disadvantage of Die casting process
Die casting is characterized by high dimensional accuracy and allows for the mass production of thin-walled metal casting products with complex shapes. Die casting also has the advantaged of producing excellent casting surface and requiring less machining process. But die casting technique is limited to the use of aluminum alloys, zinc alloys and magnesium alloys. And the initial tooling cost is higher, compared with sand casting and investment casting process.
Cast iron A48 lost foam casting motor housing
Baoding Guokun also can produce the cast iron motor housing as per your drawings. If you like, please contact gina@guokuncasting.com to get the quotation.
A High Quality China Foundry!
Guokun Casting, of Baoding Hebei is an ISO 9001-2008 registered iron and steel foundry & supplier of high-quality carbon steel, cast iron and machined castings used in power, mining, railway, agricultural, tillage, truck, automobile, pump, valve, motor, pipe fittings and gear industry.
With a monthly capacity of 10,000kgs and with more than 15 years of experience ensure the short delivery and the highest valued iron & steel casting parts.
Pump casting, Valve casting, agricultural casting, aircraft casting, railway casting, road casting, motor casting, mining casting, power generation investment casting, Medical casting, marine industry casting
Baoding Guokun Machinery Co., Ltd.
Baoding Guokun Export and Import Trading Co., Ltd
Office Add: 777# Chaoyang South Street, Baoding City, Hebei, 071000, China
Factory Address: Wangdu County, Baoding City, Hebei, 071000, China
Website: www.metalcastingfactory.com
Tel: 86-312-5951319 Fax: 86-312-5951296
Phone: 86-181 3278 9710 (WhatsApp & WeChat)
Email: gina@guokuncasting.com